Cylindrical printing simplified
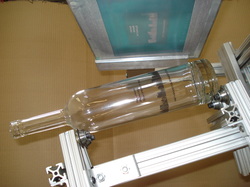
Henry L. Newman
Printing cylindrical and slightly tapered items is not difficult with the right equipment and technique. It is almost impossible to print a cylindrical item (let’s not call them round) without a machine that can hold the squeegee and screen accurately as described below. “Friction printing” is the most basic technique for printing cylindrical objects that are solid enough to be supported on four wheels or rollers. All that is needed is a fixture to support the item being printed underneath away from the print area allowing it to spin or turn true, much like cutting on a lathe. Tooling can also be made to hold the ends but “adjustable roller ware-holders” don’t require special tooling. The following outlines three general steps to simplify any cylindrical printing application;
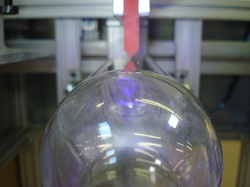
STEP 1- SQUEEGEE CENTERED with cylinder being printed.
Once the item to be printed is turning true on the rollers or tooling, check the position of the squeegee to insure it is precisely centered (left and right) with the item to be printed. This is done before the screen is sandwiched between the two making it impossible to check. Shown is an 80 durometer, urethane, double bevel often called “chisel” blade. Keep in mind, unlike flat printing, this relationship will hold through the print stroke because the screen is moving across, not the squeegee*. *in some cases the squeegee will move across the screen but always with the cylindrical item being printed thus never loosing this important “center”. Also from the side, check the squeegee length to insure it at least covers more than the print height up and down. The squeegee pressure down can be adjusted once the screen and ink are in place. Too much squeegee pressure down can cause the blade to fold over, off of center, blurring the print in that direction.
Once the item to be printed is turning true on the rollers or tooling, check the position of the squeegee to insure it is precisely centered (left and right) with the item to be printed. This is done before the screen is sandwiched between the two making it impossible to check. Shown is an 80 durometer, urethane, double bevel often called “chisel” blade. Keep in mind, unlike flat printing, this relationship will hold through the print stroke because the screen is moving across, not the squeegee*. *in some cases the squeegee will move across the screen but always with the cylindrical item being printed thus never loosing this important “center”. Also from the side, check the squeegee length to insure it at least covers more than the print height up and down. The squeegee pressure down can be adjusted once the screen and ink are in place. Too much squeegee pressure down can cause the blade to fold over, off of center, blurring the print in that direction.
STEP 2- SCREEN TO CYLINDER being printed.
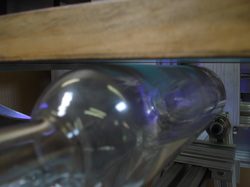
Jog the machine with the squeegee up to position
the item being printed to the screen in order to check the “off contact”. Off
contact is an even space between the screen and the item being printed and
normally is adjusted by moving the screen up and down. “On contact” works in
flat printing but rarely in cylindrical. Some printers will use thin cardboard
to check this gap. With a tightly stretched screen, the gap is a small amount,
about 1/16” of an inch. Large baggy screens when full of ink may require more
off contact. The reason for this space is to allow the squeegee to push the
screen down in a line contact, allowing a peel effect for crisp print. Too much
space between the item being printed and the screen will distort the print and
wear out the screen early. Screens if made well, can last 25,000 impressions or
more with good set-up. Because normally the screen will move across left and
right, check the off contact when the screen is right, and again when the
screen is left. Even off contact under all four corners of the screen is
important.
STEP 3- STROKE OF SCREEN before and after image.
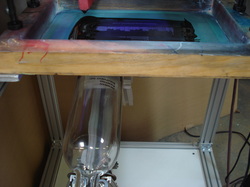
The final general area of cylindrical set-up is to adjust
the start and stop positions of the screen in relation to the artwork in the
screen. This is referred to as the screen stroke. Machines are all slightly different
but similar rules apply. The stroke will always be slightly longer than the
width of the image. The start point or right margin of the screen shown above
reveals the stroke started about one inch early before the image. This helps
get things rolling and starting early before the image is common. The photo
above shows the machine stopped after the print or the left margin. It is
important to set the stroke to stop immediately after the image ends in the screen
to prevent over rolling around more than 360 degrees and smudging the start
point of your wet print. This also helps flooding the ink back to the right
side start point usually using a second flood blade to skim slightly over the
screen never touching it on the backstroke. Most machines will print in one
direction, and flood back to this same side start point.
Once the above general steps are understood, just add ink, minimum squeegee pressure and run!
Once the above general steps are understood, just add ink, minimum squeegee pressure and run!